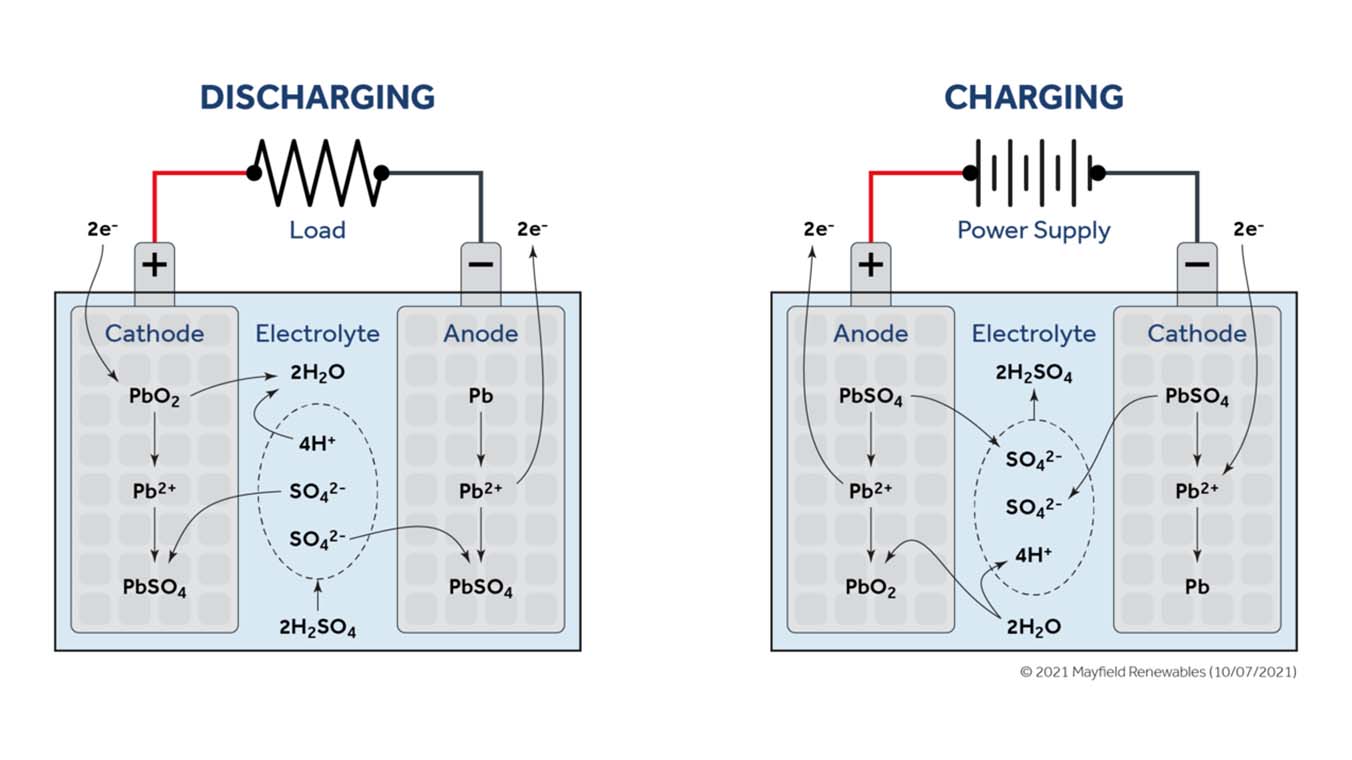
Technical Article
Lead-Acid vs. Lithium-Ion Batteries
We come across many different energy storage products in our day-to-day work designing and engineering solar-plus-storage systems. This equipment ranges from modular storage units for residential systems to massive battery packs designed for storage at the utility scale.
The industry is developing faster than ever before with respect to energy storage options, system scale, and capacity. However, despite the volume and diversity of new energy storage products, one thing remains constant: Lithium-ion and, to a lesser extent, lead-acid battery technologies continue to dominate the market. This article explains how these battery chemistries work and which common subchemistries are being used in the field today.
Lead-Acid
Lead-acid batteries are tried-and-true energy storage units that have been around for more than a century. In their simplest form, lead-acid batteries generate electrical current through an electrochemical reaction involving a lead anode and a lead dioxide cathode, separated by an electrolyte mixture of sulfuric acid and water. Anode and cathode materials are chosen in large part based on their net difference in electronegativity, or the strength of their pull on roaming electrons.
During discharge, a conductive material bridges the two electrodes, enabling electrons to flow from the less electronegative anode to the more electronegative cathode. These electrons travel through the conductive medium to an electrical load (as pictured below) and eventually to the cathode.
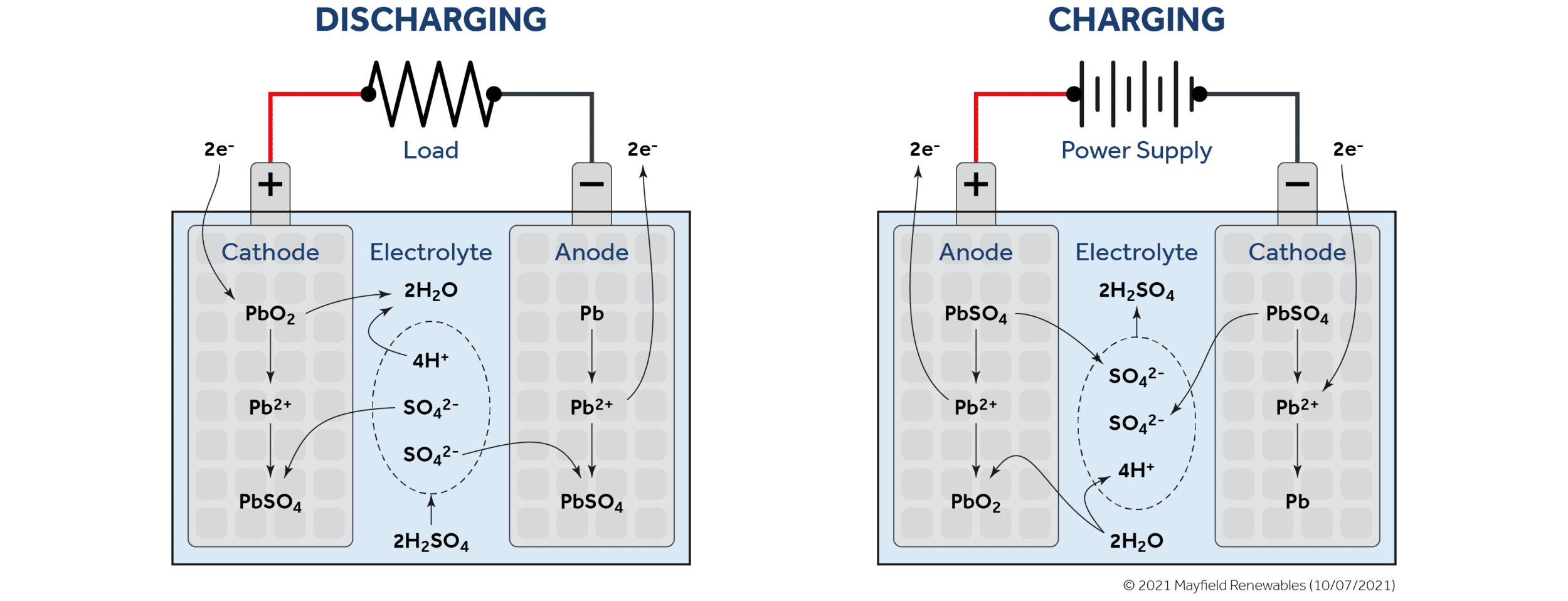
Lead-acid batteries have been and continue to be a go-to product option for projects with standby backup power. Due to their low cost but limited cycle life and depth of discharge, lead-acid batteries are well suited for situations where the battery bank will spend most of its time idle but can be relied upon for quick, temporary backup. Typical applications include emergency backup or as a stopgap during transient power outages while waiting for a backup generator to come online.
Upfront costs for lead-acid batteries tend to be cheaper—sometimes much cheaper—than alternative forms of energy storage. But that’s without factoring in their need for routine maintenance and any added costs to build an enclosure for the battery bank.
Vented enclosures for lead-acid battery banks are required by code because the cells electrolyze water, splitting H₂O into its constituent atoms when charging. A cavity filled with gaseous hydrogen and oxygen could explode under the right conditions and must, accordingly, receive sufficient air flow and ventilation.
Flooded lead-acid batteries can also experience acid stratification—a process by which sulphuric acid, which is heavier than water, gradually settles to the bottom of the cell and increases in concentration—if not cycled regularly. As the concentration of sulfuric acid increases so will the cell open-circuit voltage. This artificial voltage rise can adversely impact cell performance and speed up corrosion. Valve-regulated lead-acid batteries (commonly referred to as “sealed” lead-acid batteries) with gel or absorbed glass mat (AGM) electrolyte solutions help to minimize the chances of acid stratification and are generally safer and will perform better throughout their useful life.
Lithium-Ion
Lithium-ion batteries come in a diverse range of sizes and chemistries. However, they are commonly made with a silicon-, carbon- or graphite-based anode and a cathode with a lithium metal oxide. Lithium-ion batteries have a salt-based electrolyte and a polymer separator that allows positively-charged lithium ions, but not free electrons, to flow through it.
As pictured below, a discharging lithium-ion battery will send lithium ions from the anode to the cathode through the electrolyte solution while the electrons that have been stripped from the lithium ions get passed to the cathode through the external load. Both the ions and the electrons meet and recombine at the cathode. The entire process is reversible when an external voltage is supplied to the system.
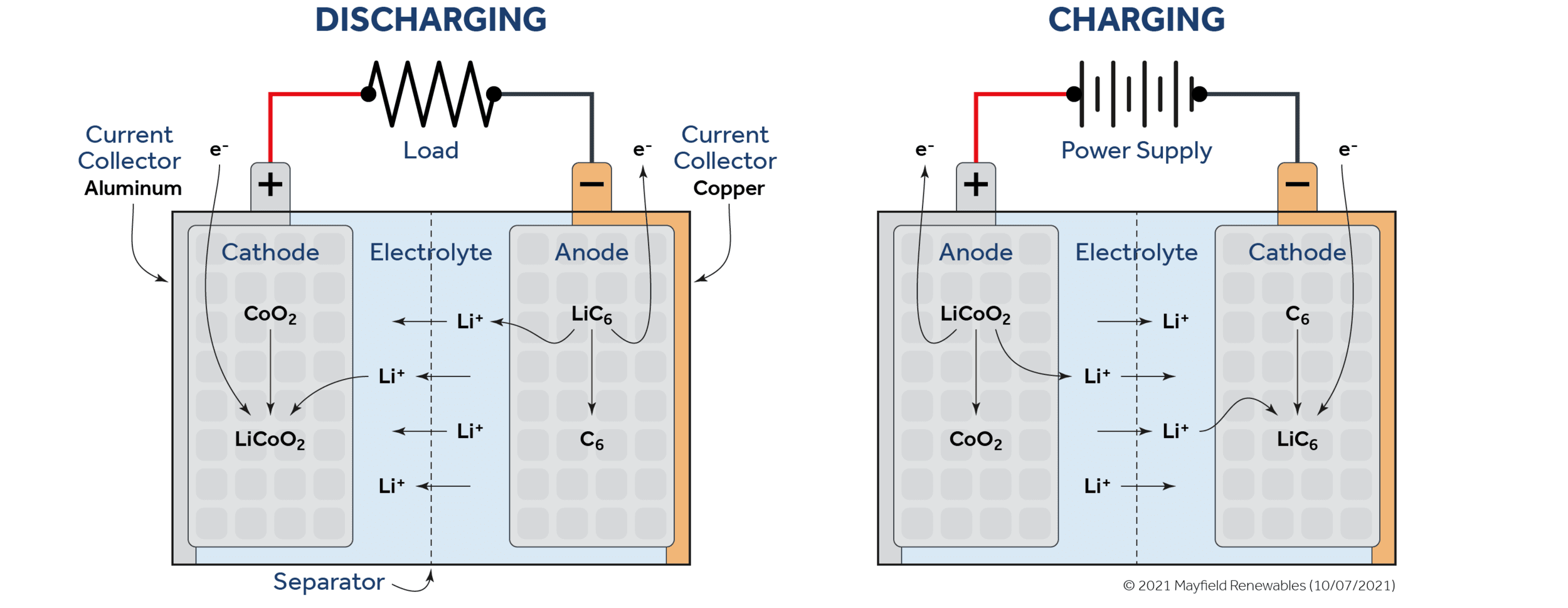
Lithium-ion technologies have progressed substantially in recent years and benefit from institutional inertia as more funds pour into energy storage R&D. Foremost among the benefits of lithium-ion chemistry is its high electrode potential (voltage), or the difference in electron attraction between the materials that make up its anode and cathode.
Due to lithium-ion’s inherent chemical advantages, incremental changes in manufacturing can lead to significant performance improvements. For example, at a recent Tesla Battery Day, Tesla announced that they had improved battery current throughput by simply increasing the electrical contact size. This change can be implemented immediately at scale without altering cell chemistry.
Beyond their chemical advantages, the methods of production for lithium-ion batteries are well established, which minimizes new variables when switching between chemical variants. Production can still be expensive, however, and is subject to supply chain disruptions as China mainly controls the supply of many components.
Use cases for lithium-ion batteries depend largely on cell chemistry. Let’s run through some of the most common types available today.
Lithium-Iron-Phosphate (LFP)
LFP cells are among the most fire-safe options in the lithium-ion battery family. While LFP cells are capable of off-gassing, they can be punctured or even crushed without inducing flames. This safety comes at the expense of a lower c-rating (meaning power cannot be drawn from the cells as quickly as other chemistries) but also retains a reasonably high energy density, a very high cycle life, and a full depth of discharge.
Beyond LFP’s electrical advantages is its lower cost of materials: Iron is abundantly available and affordable for manufacturers. By pairing adequate performance with low cost with exceptional fire safety, LFP batteries are expected to lead the grid-storage market by 2030.
Lithium-Nickel-Manganese-Cobalt (NMC)
NMC cells can be found inside Tesla Powerwalls, LG Chem batteries, and many electric vehicles on the road today. Their chemical makeup yields a higher energy density than LFP cells without significant decreases in power output or cycle life. Like LFPs, NMCs can also be fully discharged. However, unlike LFPs, NMCs may induce flame during thermal runaway and pose a fire risk if not properly manufactured, protected, and maintained.
According to Wood MacKenzie, NMCs have historically dominated grid storage, to the tune of 70 percent market share in 2015. But, as noted above, LFPs are quickly gaining grid-storage market share and are expected to overtake NMCs this decade. This shift is in part a move away from battery cells prone to flaming during thermal runaway, and also due to their chemical makeup as cobalt is expensive to procure and can be toxic when released into the environment.
Lithium Titanate Oxide (LTO)
LTO cells are less common in large power systems but nonetheless offer distinct advantages over other chemistries. With a wider operational temperature range, very low thermal runaway risk, high cycle life, and very high C-rating (on the order of the typical power draw from a capacitor), LTOs are popular for short-duration, high-power uses such as model airplanes or as a carry-over for data centers waiting for generators to warm up. However, fast, high power output isn’t free and comes at the expense of depth of discharge, which maxes out at about 60%. Currently, LTOs are typically used in EVs and e-bikes. As costs come down and the ESS market diversifies, they could find a niche in industrial settings with a need for high power density.
Author Matthew Robertson is a chemist by training and a solar-plus-storage system designer by profession. To get in touch with Matthew, or to start a solar-plus-storage design project, contact us here.